1.离型纸基本特性
1.1离型纸概念
1. 2 离型纸分类
1.2.1 淋膜离型纸
1.2.2 格拉辛离型纸
1.2.3 CCK 离型纸
1.2.4 皮革离型纸
1.2.5 其他离型纸
1.3离型剂
离型纸的技术指标主要有以下几个:硅油涂布量,离型力(剥离力),残余粘着率及硅酮覆盖效果(染色测试)。
硅油涂布量是指离型剂涂布在材料上的量,单位是 g/m2。一般溶剂型硅油的涂布量为 0.30~0.80g/m2,无溶剂型硅油的涂布量为0. 80~1.30g/m2。需要专业的测试设备才能测试涂布量,如X-射线荧光光谱仪(XRF)。硅油涂布量直接影响到离型(剥离)性能。较高的涂布量,能够密实地将原纸覆盖,保证硅油均匀分布。而较低的硅油涂布量,则容易出现漏涂等现象,导致剥离不良。
1.4. 2 离型力
离型力(剥离力)是指为了分离涂有胶黏剂的面材与离型底材或其他离型材料,在特定的条件及一定的剥离角度与剥离速度下所需要的拉力。剥离力太低会导致标签成型或贴标时飞标,剥离力太高会导致在模切排废中断卷或在自动贴标时不出标。离型力一般测试常温离型力和老化离型力。常温离型力是在常温下通过标准测试方法得到的离型力数据,单位是 N/25mm,可以转换成 g/25mm。
0.10N/25mm,即10g以下的剥离力,俗称为轻剥离;
0.20N/25mm,即20g以下的剥离力,俗称为中剥离;
0.35~0.45N/25mm,即35~45g的剥离力,俗称为重剥离;
0.60~0.80N/25mm,即60~80g的剥离力,俗称为重重剥离;
当然也有 0.03~0.04N/25mm,即 3~4g 的剥离力,俗称为轻轻剥离;
也有 1.00N/25mm,即 100g 以上的剥离力,俗称为超重剥离。
老化离型力,标准测试方法为70±5℃烘箱老化20h后测得的离型力数据,一般较常温离型力略大。
1.4. 3 残余粘着率
残余粘着强度,是指胶粘剂面材在指定条件下与离型底纸先接触,之后将其贴在标准测试板上制成标准试片,然后在固定的剥离角度、速度下,从标准试片上将其剥离时所需要的力。而残余粘着率是以百分比表示的,是将上述胶粘剂面材残余粘着强度比上同一面材在不接触离型底纸前提下与标准测试板贴合所产生的粘着强度的比值。残余粘着率主要反映硅油固化的效果。
UV 固化硅油的残余粘着率一般为100%,热固化硅油的残余粘着率最高为90%。如果发生脱硅情况,离型纸的残余粘着率一般不会超过70%。
硅酮覆盖效果——水溶性染料染色测试是评估离型剂涂布覆盖质量的方法,该方法主要用于以纸张为基材的离型剂涂布,且该基材接触染料后会有颜色改变。包括使用一定量的染料溶液在一定的时间内润湿离型纸,用擦拭纸吸除染料,再使之干燥,其覆盖质量以眼睛目测做定性评估或以色差仪做定量评估。假如离型剂涂布不均或涂布量太低,基材中的纤维就会与染料接触而使该区域呈现深色反应,该区域是染料被基材吸附造成颜色的变化。一般而言,离型纸与染料接触产生的颜色越深,离型剂的覆盖效果越差。
1.5 离型纸的选用
离型纸的硅油涂布量直接影响到胶水的适用性,水胶需要较低的硅油涂布量,而油胶和热熔胶则需要较高的硅油涂布量。
涂胶厂一般选用高涂布量的离型纸,而复合厂一般选用中等涂布量的离型纸,若是热复合,也需要选择高涂布量的离型纸,保护膜(水胶)仅需要低涂布量的离型纸即可,中等涂布量的离型纸适合油胶保护膜使用,高涂布量的离型纸不适合保护膜使用。
由于气候的关系,模切厂冬季宜选用剥离力偏重的离型纸,夏季宜选用剥离力偏轻的离型纸。有些特殊需求的胶带,在模切过程中使用的离型纸,需提前跟离型纸供应商沟通,在作深度测试、对比后方可进行生产,否则将会产生大量废品。
2.离型纸生产工艺
在线乳液硅油涂布分为纸机在线涂布乳液硅油和 PET 薄膜在线涂布乳液硅油两种。
目前比较成熟的纸机在线涂布乳液硅油技术主要用于生产烘焙纸和卫材离型纸。纸机在线乳液硅油涂布烘焙纸一般在施胶部进行离型剂涂布,生产时对纤维和打浆度有一定的要求,车速较慢。烘焙纸没有离型力指标要求,一般是在烤箱中检测实际粘着量为准,产品为双面离型纸(实际使用容易混淆),需符合食品标准,同时要求不易变黄。
纸机生产卫材用离型纸对离型力要求较高,一般采用双涂布头方式:施胶部先涂布封闭层,再涂布乳液硅油离型剂。封闭层涂布后若进行压光可提高离型效果,产品离型力约在20~40g/25mm左右。
表1是A和B两公司提供的纸机在线涂布乳液硅油纸样的测试数据。
PET 薄膜在线乳液硅油产品是 PET离型膜的发展方向,在拉膜前进行乳液硅油涂布,涂布量可以,控制低到 0.2g/m2左右。目前国内进口日本三菱的产品比较多,主要用在水晶标领域,现在也开始有厂家尝试生产在线乳液硅油涂布 PET薄膜产品。
这类产品主要是纸类基材进行乳液型硅油涂布。由于增加一道涂布加工工序,因此成本相对较高,据了解目前国内只有一家工厂生产,且产量不大。我单位尝试过在基材上涂布乳液型硅油,表2为测试数据。与表1 对比看,五个纸样的离型力数据均较高,达不到纸机上涂硅的水平。
这类生产工艺的基材一般采用特殊纸张或膜类。
纸类基材主要为格拉辛、PEK、CCK、SCK 等封闭性较好的纸张,硅油主要采用溶剂型或无溶剂型硅油。这种工艺是目前生产标签离型纸的主要形式,工艺技术成熟,产品广泛应用于不干胶标签、双面胶带、碳纤维制品等领域。
薄膜基材分耐温型和不耐温型两种。由于溶剂和无溶剂型硅油均需要高温固化,因此这类基材只能选能耐高温的PET薄膜,厚度从12pm到150pm不等,主要用于不干胶、电子电器、鞋材离型等领域。
UV 固化硅油基材选择不耐高温的 PE 薄膜,主要用于卫材领域,是目前的UV硅油增量的主要部分。
原纸底涂隔离层再涂布离型剂的离型纸是国内的主要形式,广泛用于卫材、快递单等领域。由于不同需求,原纸质量相差较大,卫材领域要求较高,其他领域则可以使用质量较差的牛皮纸等。
底涂用隔离剂有PVA和胶乳两种。涂布量一般在1~2g/m2。要求涂布后成膜性较好,对硅油有良好的防渗透作用。
硅油离型剂有溶剂型和无溶剂型。溶剂型产品有缩合型和加成型两种,溶剂缩合型由于采用有机锡为催化剂,其残留对人体皮肤有害,在卫材领域禁止使用,但由于低成本的优势,目前仍有一些厂家生产。溶剂加成型产品由于对黏度的限制不严格,可以使用较大分子链的产品,采用较低的涂布量仍可保持较小的离型力,其涂布量可以低至0.3g/m2,低的涂布量保证其对无溶剂型产品的成本优势。无溶剂型硅油产品由于无溶剂的污染和安全生产的保障,加上涂布设备的发展,是今后的发展方向。
采用在原纸上底涂隔离剂再涂布乳液硅油的方式,据了解有脱硅的风险,目前很少有厂家使用。
原纸经淋膜后,在淋膜面上涂布离型剂,生产而得离型纸。淋膜纸是将纸作为基体,采取特殊的工艺,将PE(聚乙烯)、PP(聚丙烯)塑料附着在上面形成的复合纸。因为纸张表面有纸毛及纤维,所以淋膜必须到一定的量,才能保证没有硅油渗透点而导致剥离不良。一般淋膜纸的淋膜量为16g/m2,据说温州地区已经能做到11~13g/m2,相当接近国外先进设备的淋膜数据。理论上说,只要能够保证胶带从离型纸上剥离,再低的淋膜量都是可以的。淋膜离型纸一般选用全木浆纸,特别是电子行业。如果选用草浆纸,在模切的时候就会有很多纸屑及容易破边。全木浆纸又称为牛皮纸,比如本色牛皮纸(俗称本牛)、白色牛皮纸(俗称白牛)、黄色牛皮纸(俗称日本黄彩牛)、蓝色牛皮纸(俗称印尼蓝彩牛)。当然也有用全木浆的双胶纸做原纸的,更有用照相纸做原纸的,以及用铜版纸及白板纸、牛卡纸、牛奶卡纸做原纸的。只要淋膜的纸塑牢度能够达到要求,淋膜没有渗透点,均匀平整,什么纸都可以用来做淋膜原纸。
传统的聚烯烃淋膜纸的加工工艺一般是利用挤出机将聚烯烃离子高温热熔后挤出在底纸上形成淋膜,昆山福泰的张言波等发明了一种新的淋膜纸的加工工艺,即将聚烯烃乳液(包括PE和PP乳液)直接涂布于原纸上,干燥后再在淋膜纸上涂布离型剂制得离型纸。
这种生产工艺由于采用聚烯烃等石化产品进行淋膜,造成纸张再回收利用困难,其结果会造成环境污染,另由于石化产品价格不断上涨,渐渐地没有了价格优势,终将被市场淘汰。
随着科学技术的发展,人们生活水平的提高,离型纸的需求将会越来越广,人们对离型纸的要求也会越来越高,不管是哪种生产工艺和技术,在保证离型力的情况下降低生产成本、减少上机次数才是最佳选择。从离型纸的使用效果看,降低离型剂的使用量来保证离型力是关键。这就要求研究者们不断创新、不断改革,将离型纸的事业不断推向前进。
原文始发于微信公众号(楷塑科技):离型纸及其生产工艺分析
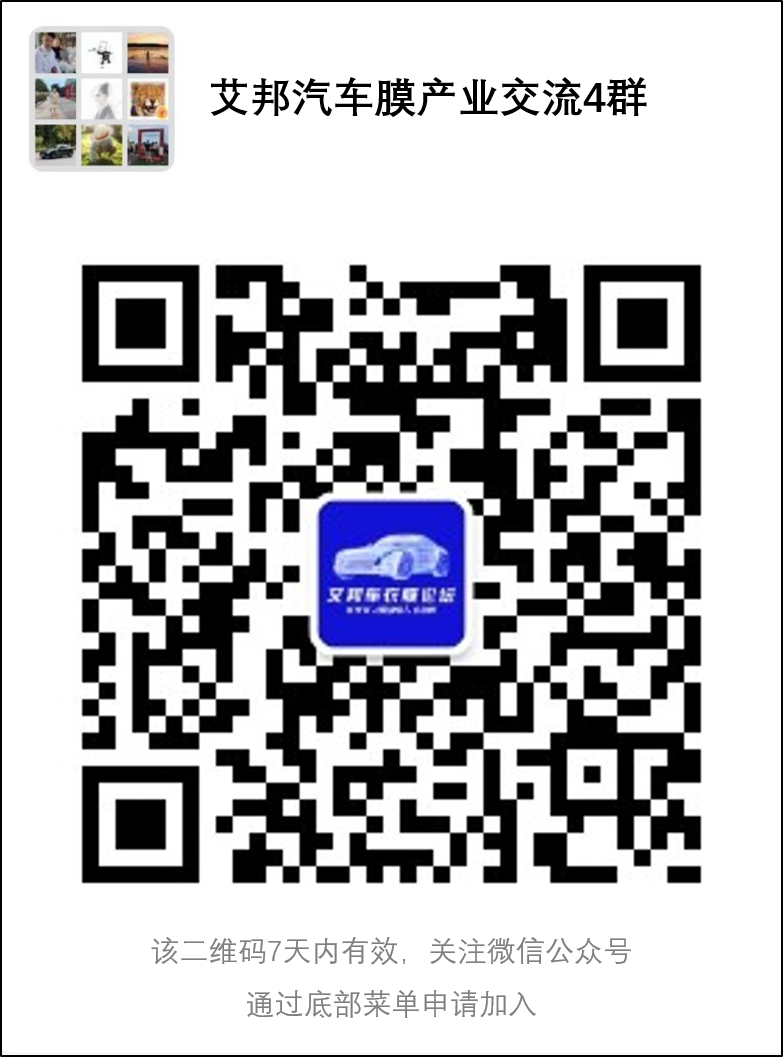